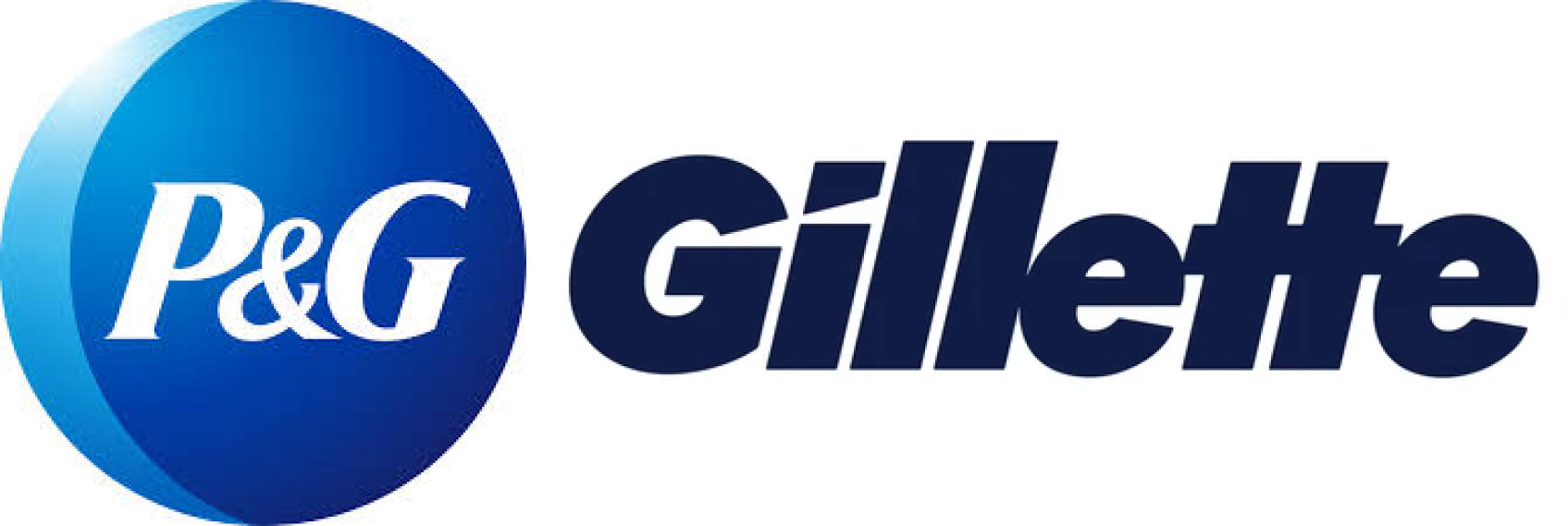
Mechanical Engineering Placement
April - September 2024
1. Using Data Analytics to Identify Automation Opportunities
I used data analytics to identify opportunities for automating existing production lines. This process included two visits to the factory in Poland to gain a thorough understanding of the current operations and attending the UK Automation Show to see the latest technology and engage with potential suppliers. Based on my findings, I developed functional specifications for the proposed automation, shared them with vendors, and gathered budgetary quotations. I then conducted a financial analysis and presented the potential cost savings and rate of return to global leadership.
2. Analysing Existing Lines and their Potential to be Converted to using Sustainable Materials
I analysed the existing production lines to assess their potential for being converted to sustainable materials, identifying the necessary tooling changes and defining the required packaging parameters for Gillette’s current product range. This process also involved understanding the relevant legislative sustainability requirements, such as the EUGD, alongside Procter & Gamble’s own sustainability goals.
3. Building a Simulation Tool to Predict Theoretical Buffer Sizes
During this project, I was onboarded to a new simulation software and programming language and used it to build a tool that can predict theoretical buffer sizes. I reviewed the model with members of my immediate team and US-based modelling experts. This model adds to Gillette's digital tools and is designed to reduce the number of expensive tests required to quantify buffer capacity.
4. Improved the Packaging Equipment Database
I supplemented the database with photos, videos and serial numbers of packaging equipment which I collected on-site in Poland as well as by contacting global plants. This improves data on existing lines, standardises communication between plants and assists with tracking of machine movement. In the longer term, the databases simplify the reapplication of existing equipment to new lines.
5. Create a Scaled Model of an Existing Product for Career Fairs
This group project involved printing and finishing a scaled-up model of a Gillette razor. I was onboarded to 3D scanning tools and multi-material 3D printers. I then collected data from potential users to identify what features were of interest. The model will be brought to career fairs to add an interactive element while showcasing the range of roles available.
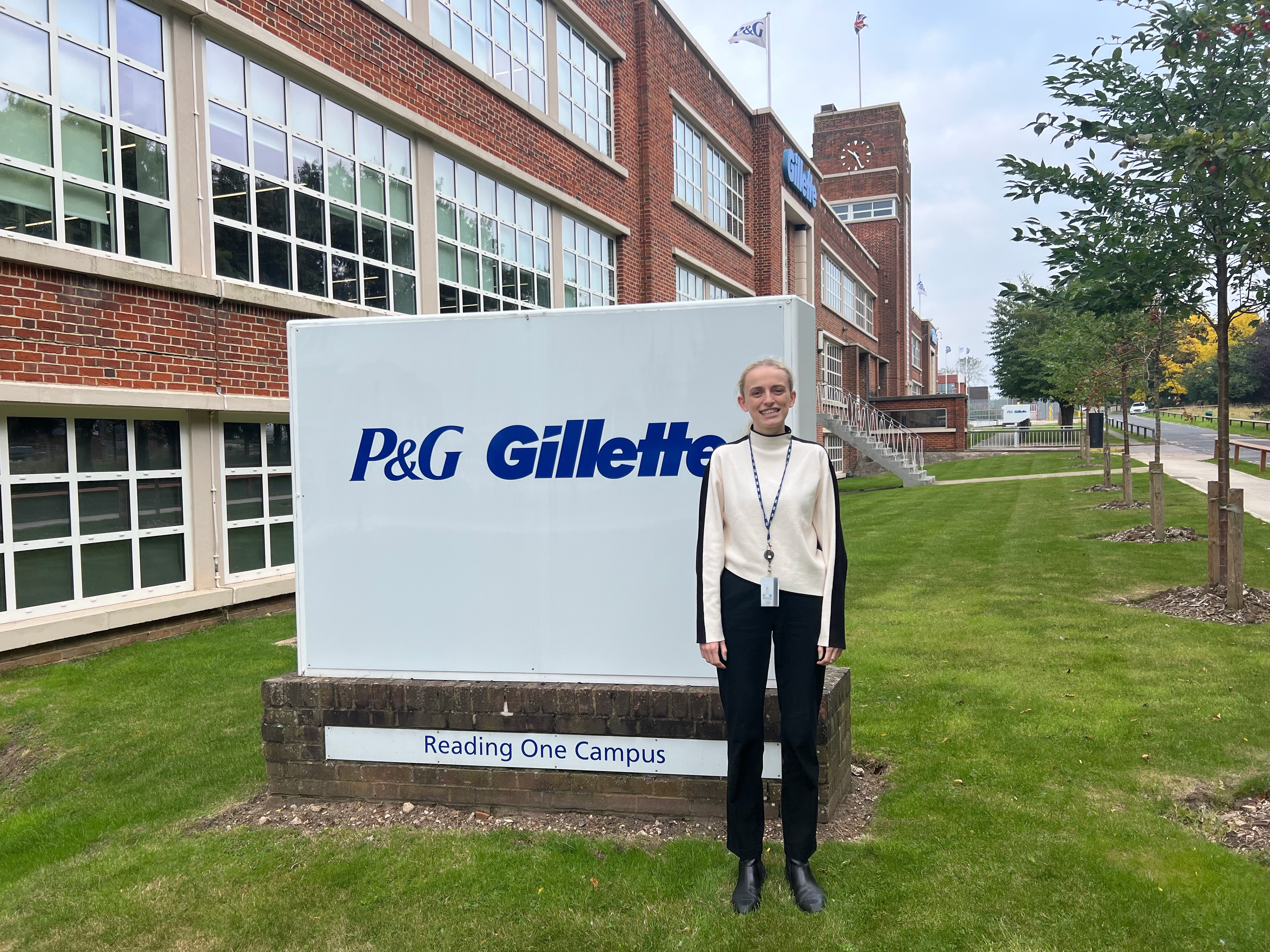