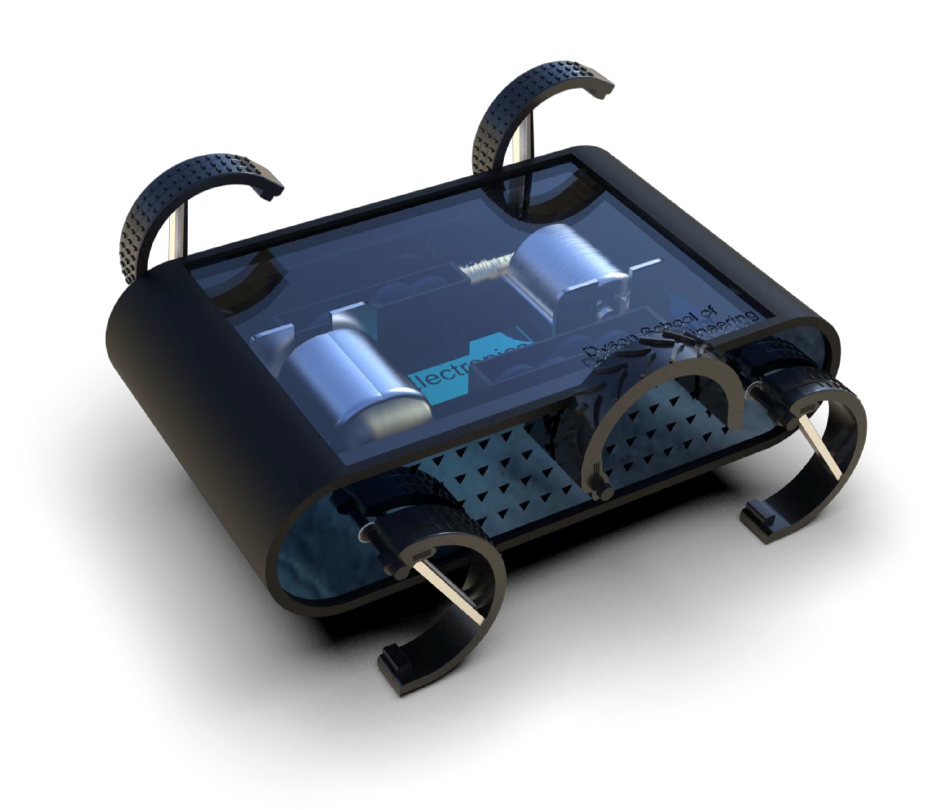
The RHex, a bio-inspired six-legged robot, is commercially manufactured by Boston Dynamics. It is specifically designed to endure challenging environmental conditions and navigate rugged terrains with ease. The RHex Mini, a smaller derivative of the original, retains many of the same design principles while focusing on making robotics education more accessible and affordable.
This project involves designing an RHex Mini that adheres to a predefined set of specifications.
Specification
1. Body - Length ≤ 165 mm, Height ≤ 40 mm, Width ≤ 100 mm
2. Leg - Length ≤ 50 mm, Radius ≤ 35 mm
3. Mass - 300 g
4. BoM Cost ≤ 100 GBP
5. Turning Circle ≤ 165 mm
6. Payload ≥ 300 g
Required Capabilities
1. Speed ≥ 0.5 m/s
2. Drop Height ≥ 300 mm
3. Climb Obstacles ≥ 200 mm High
Material Selection
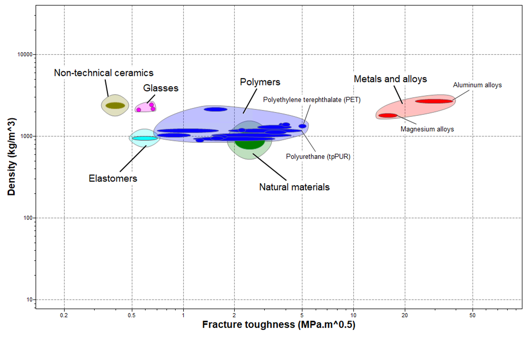
Constraints:
Density ≤ 4000 kg/m^2
Cost ≤ 67 GBP/Kg
Aluminium alloys were chosen for the body due to their low density, ensuring the structure is lightweight while maintaining high fracture toughness, which minimizes the risk of damage in collisions. Additionally, aluminium provides excellent corrosion resistance and shock absorption capabilities.
Engineering Analysis - Body
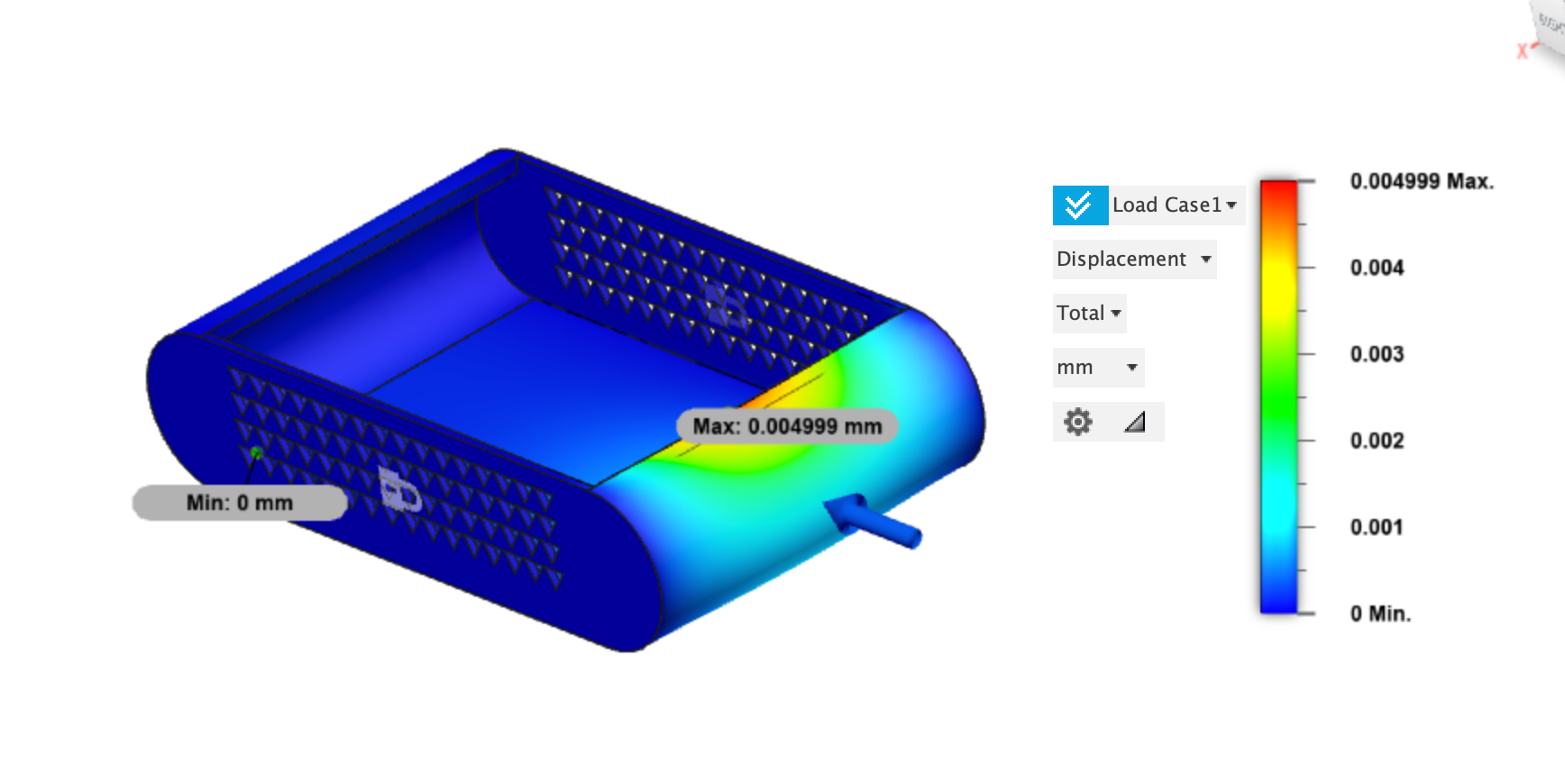
Analysis of body w/o rubber seal
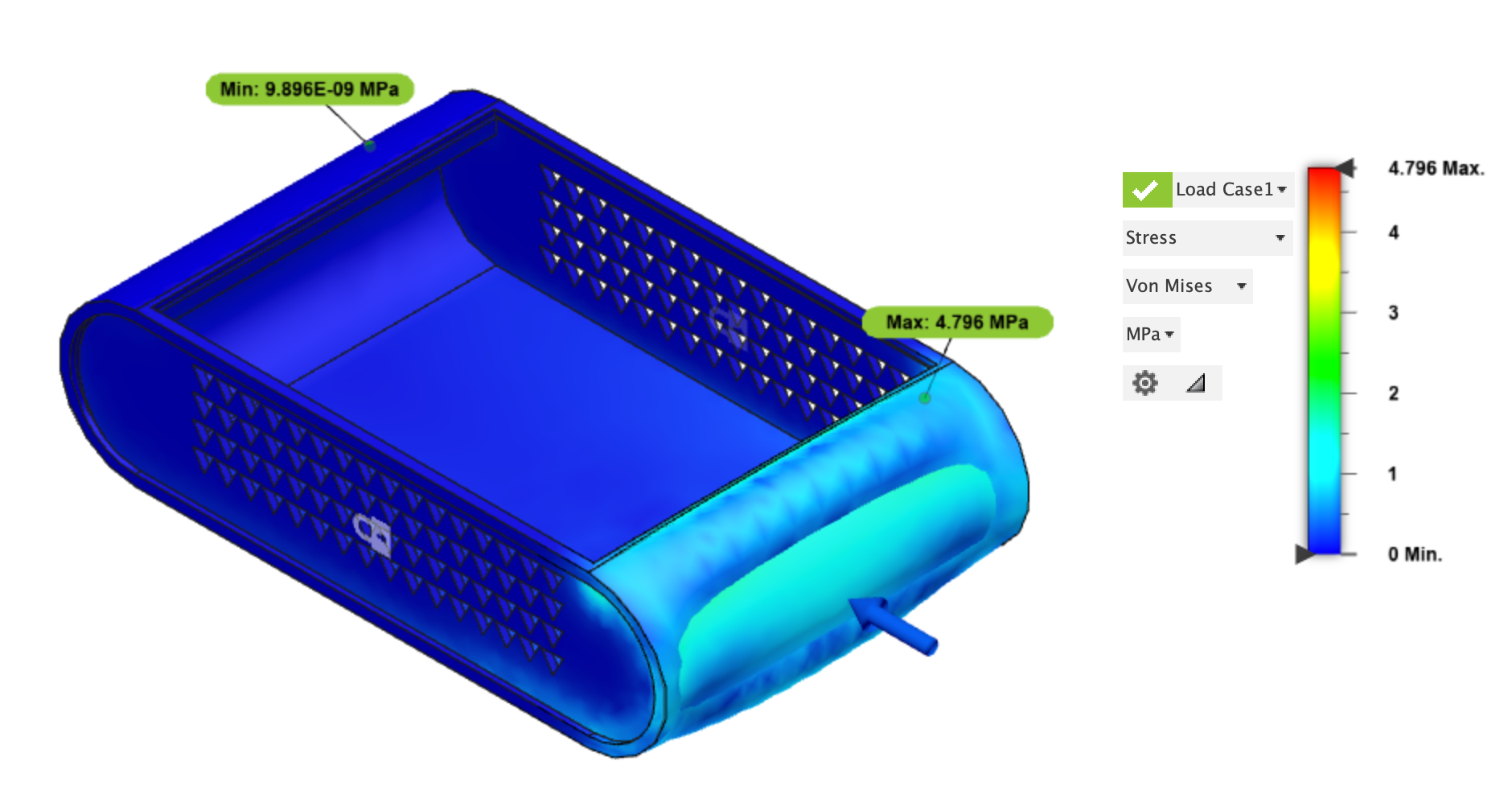
Analysis of body w/ rubber seal
The drop test validated that the rubber seal would protect the body from permanent deformation.
Without the rubber seal the aluminium body does not fail however, it is permanently deformed at the nose of the unprotected body near the joint between the body and lid.
Engineering Analysis - Legs
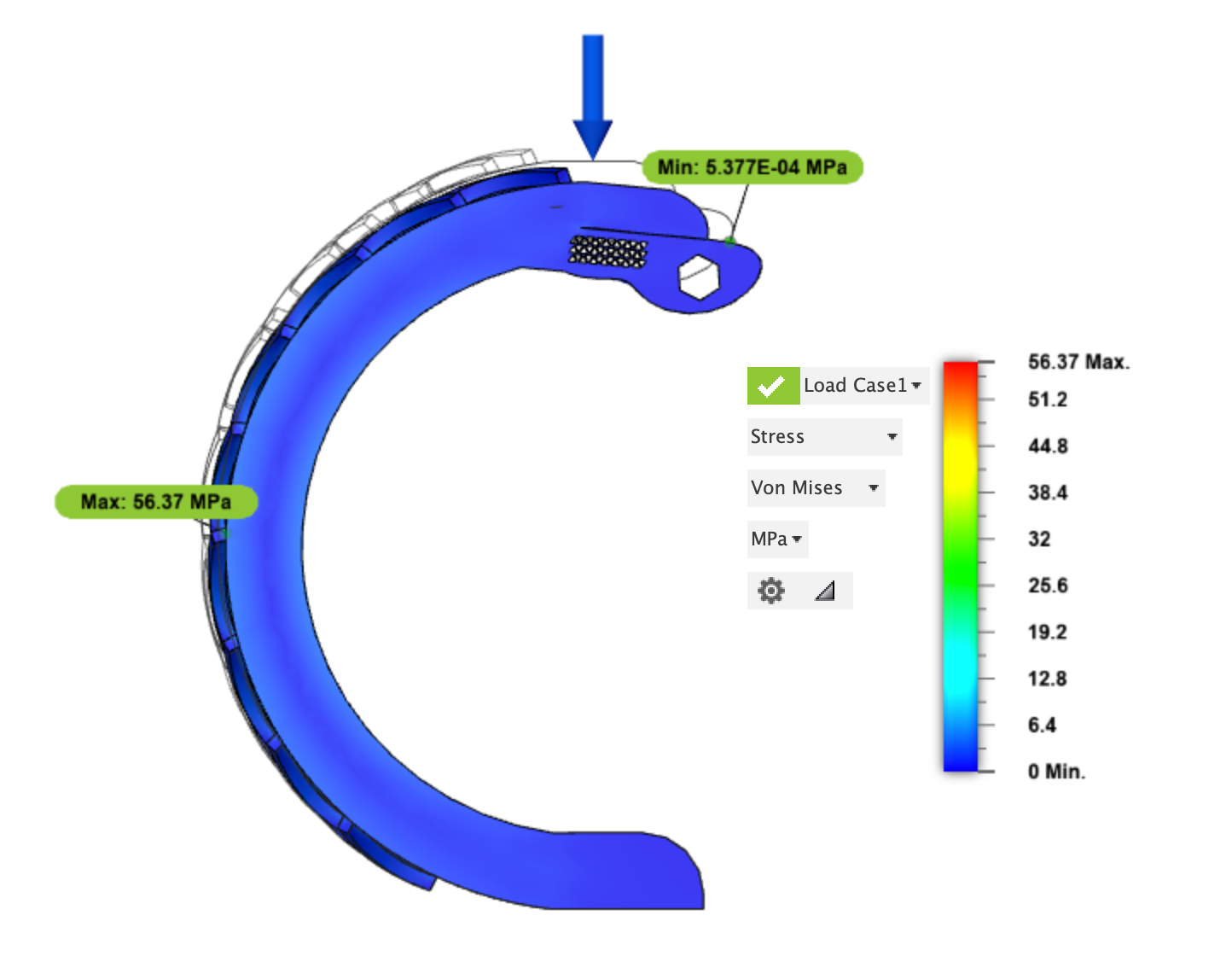
Central Legs
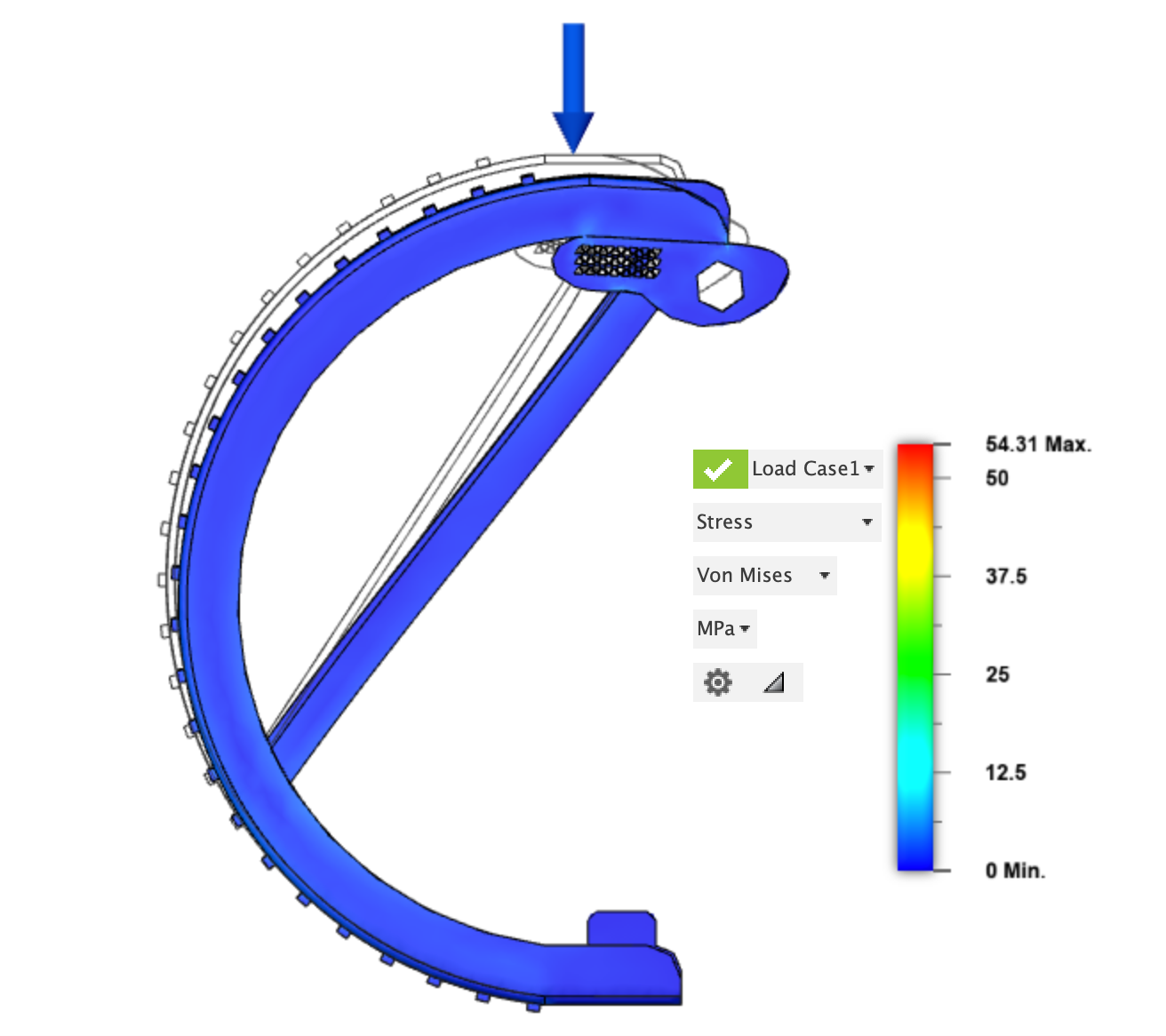
Front/Rear Legs
Central Legs - The initial analysis showed that the leg could support the 6N force, though a risk of failure was still identified. This failure was likely due to excessive bending under the load. To significantly reduce this risk, the thickness of the leg arc was increased by 2 mm throughout. This adjustment resulted in a 71% reduction in the maximum stress experienced by the leg.
Front/Rear Legs - To model the forces acting on the three-bladed mechanism, a 6N load was applied to a single blade, simulating the worst-case scenario where one blade (i.e., one-third of a front leg) bears the entire weight of the robot. Similar to the analysis performed on the single-bladed legs, the results showed that the structure could withstand the force. However, there was a risk of component failure due to excessive bending. To address this, the thickness of the supporting tendons was increased, resulting in a 22% reduction in the maximum stress experienced by the blade.
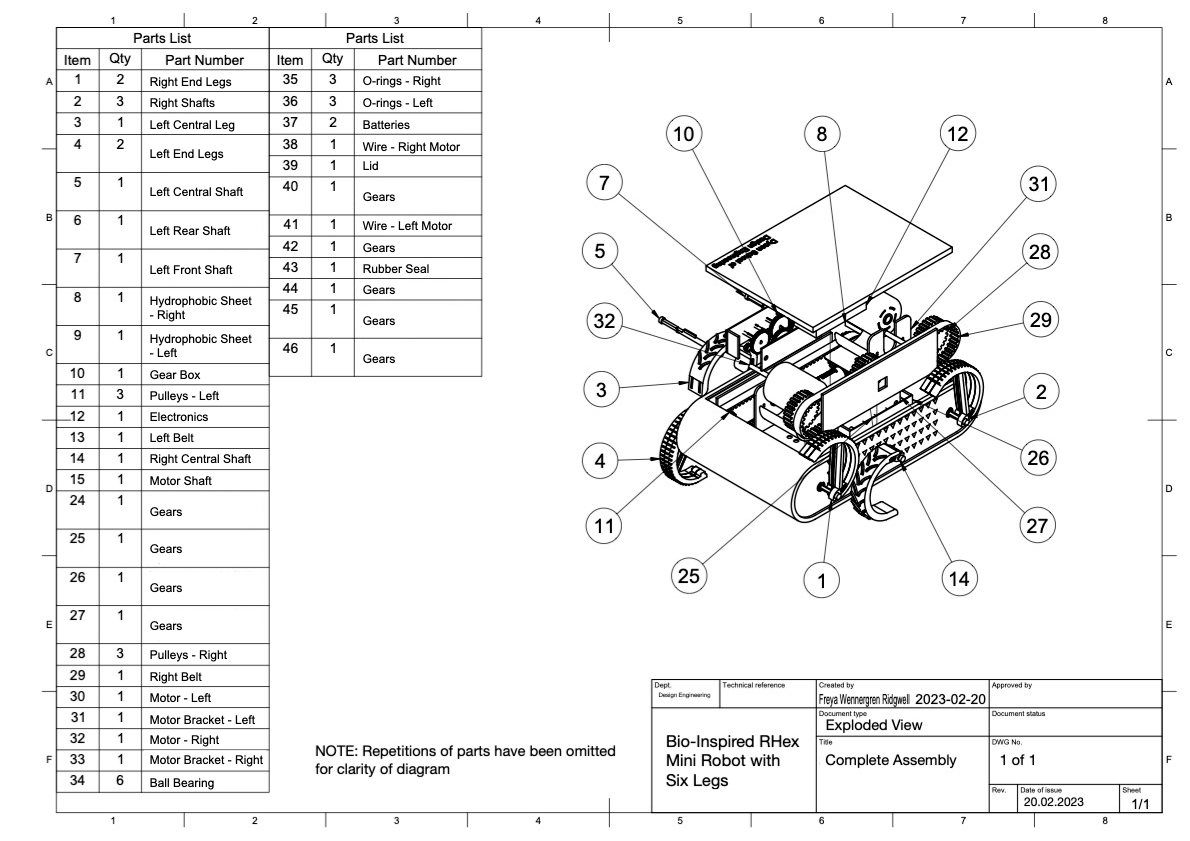
Exploded Diagram Engineering Drawing